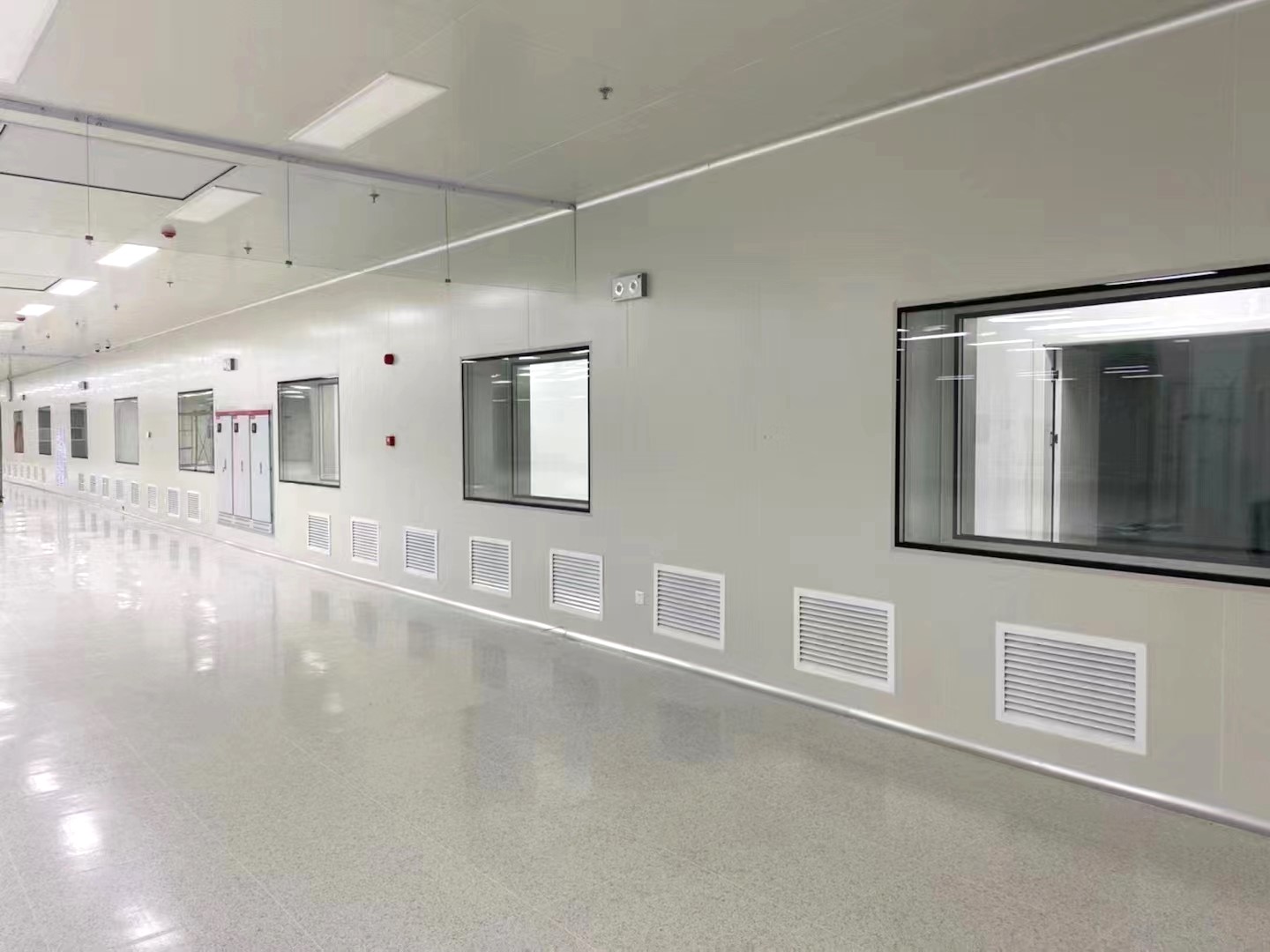
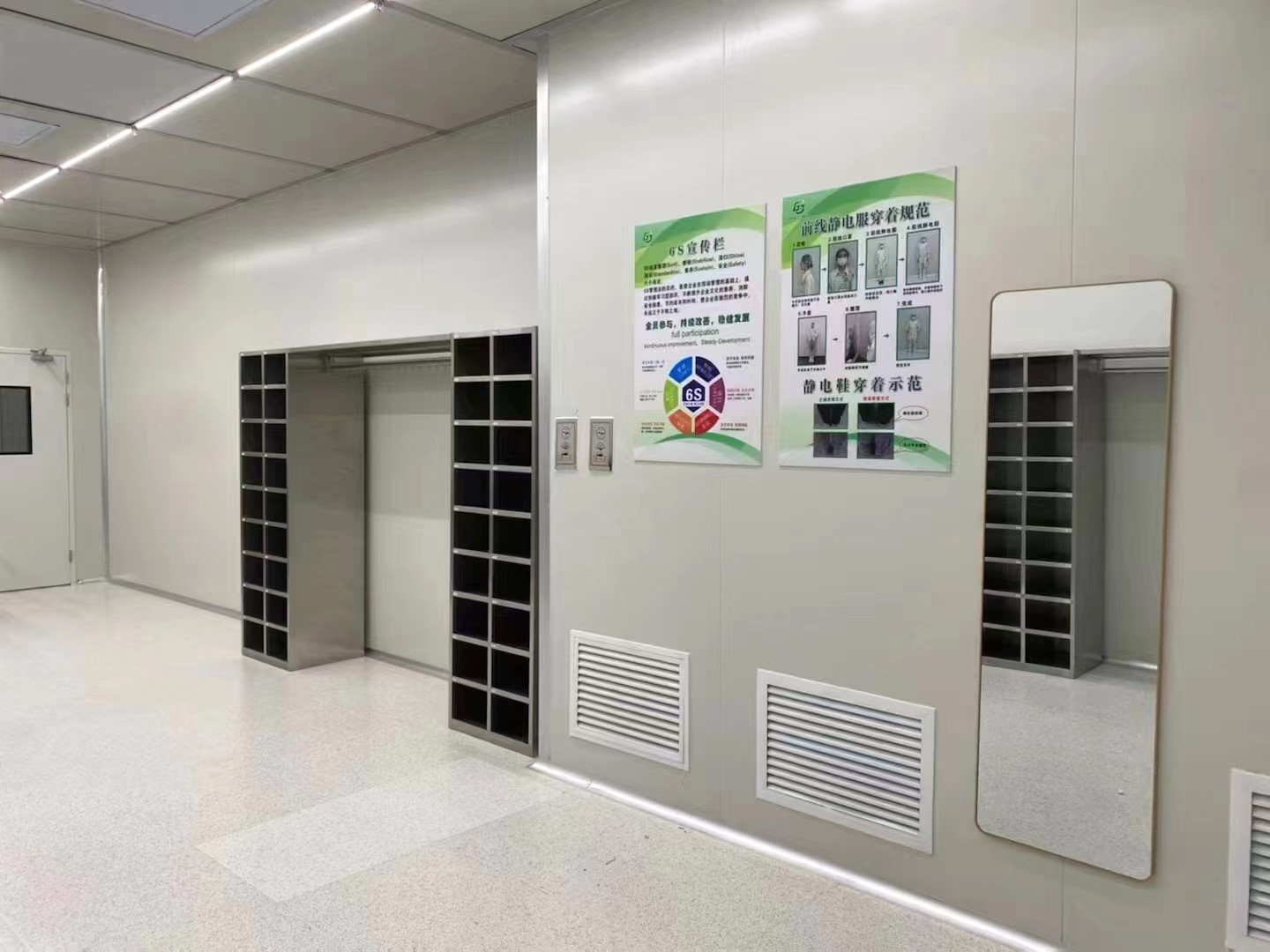
Elektronische productie -industrie:
Met de ontwikkeling van computers, micro -elektronica en informatietechnologie heeft de elektronische productie -industrie zich snel ontwikkeld en is de Clean Room -technologie ook aangedreven. Tegelijkertijd zijn hogere vereisten naar voren gesteld voor het ontwerp van een schone kamer. Het ontwerp van een schone kamer in de elektronische productie -industrie is een uitgebreide technologie. Alleen door de ontwerpkenmerken van de schone kamer in de elektronische productie -industrie volledig te begrijpen en redelijke ontwerpen te maken, kan de defecte producten in de elektronische productie -industrie worden verminderd en de productie -efficiëntie wordt verbeterd.
Kenmerken van een schone kamer in de elektronische productie -industrie:
De vereisten van het netheidsniveau zijn hoog en het luchtvolume, temperatuur, vochtigheid, drukverschil en uitlaat van apparatuur worden indien nodig geregeld. De verlichting en luchtsnelheid van de sectie Clean Room worden geregeld volgens het ontwerp of de specificatie. Bovendien heeft dit type schone kamer een extreem strikte vereisten voor statische elektriciteit. De vereisten voor de luchtvochtigheid zijn bijzonder ernstig. Omdat statische elektriciteit gemakkelijk kan worden gegenereerd in een overdreven droge fabriek, veroorzaakt dit schade aan de integratie van CMOS. Over het algemeen moet de temperatuur van een elektronische fabriek worden geregeld op ongeveer 22 ° C, en de relatieve vochtigheid moet worden geregeld tussen 50-60% (er zijn relevante temperatuur- en vochtvoorschriften voor speciale schone kamer). Op dit moment kan statische elektriciteit effectief worden geëlimineerd en kunnen mensen zich ook op hun gemak voelen. Workshops voor chipproductieproductie, workshops voor een cleanruimte van geïntegreerde circuit en schijfproductie zijn belangrijke componenten van de schone kamer in de productie -industrie van elektronica. Aangezien elektronische producten een extreem strikte vereisten hebben voor de omgeving van binnenlucht en kwaliteit tijdens de productie en productie, richten ze zich vooral op het beheersen van deeltjes en drijvend stof, en hebben ze ook strikte voorschriften voor de temperatuur, vochtigheid, fris luchtvolume, lawaai, enz. .
1. Geluidsniveau (lege toestand) in de Klasse 10.000 Clean Room van een elektronische productie -fabriek: mag niet groter zijn dan 65dB (A).
2. De volledige dekkingsverhouding van de verticale stroming Clean Room in Electronics Manufacturing Plant mag niet minder zijn dan 60%, en de horizontale unidirectionele stromingsruimte moet niet minder zijn dan 40%, anders zal het een gedeeltelijke unidirectionele stroom zijn.
3. Het statische drukverschil tussen de schone kamer en het buitenleven van de elektronica-fabriek moet niet minder zijn dan 10 pa, en het statische drukverschil tussen het schone gebied en het niet-spleetgebied met verschillende luchtreinigheid moet niet minder zijn dan 5Pa .
4. De hoeveelheid frisse lucht in klasse 10.000 Clean Room of the Electronics Manufacturing Industry moet het maximum van de volgende twee items nemen:
① Compenseer de som van het binnenuitlaatvolume en de hoeveelheid frisse lucht die nodig is om de positieve drukwaarde binnenshuis te behouden.
② Zorg ervoor dat de hoeveelheid verse lucht die wordt geleverd aan de schone kamer per persoon per uur niet minder dan 40m3 is.
③ De kachel van het airconditioningsysteem van de schone kamer in de elektronische productie-industrie moet worden uitgerust met verse lucht en over-temperatuurvermogen. Als er puntbevochtiging wordt gebruikt, moet waterloze bescherming worden ingesteld. In koude gebieden moet het frisse luchtsysteem worden uitgerust met antivriesbeveiligingsmaatregelen. Het volume van de luchttoevoer van de schone kamer moet de maximale waarde van de volgende drie items innemen: het volume van de luchttoevoer om te zorgen voor het niveau van de luchtinheid van de schone kamer van de elektronische productie -fabriek; Het volume van de luchttoevoer van de schone kamer van de elektronische fabriek wordt bepaald volgens de berekening van de warmte- en vochtbelasting; De hoeveelheid frisse lucht geleverd aan de schone kamer van de elektronische fabriek.
Biomanfabricage -industrie:
Kenmerken van biofarmaceutische fabrieken:
1. Biofarmaceutische cleanroom heeft niet alleen hoge apparatuurkosten, complexe productieprocessen, hoge vereisten voor netheidsniveaus en steriliteit, maar hebben ook strikte vereisten voor de kwaliteit van productiepersoneel.
2. Potentiële biologische gevaren zullen verschijnen in het productieproces, voornamelijk infectierisico's, dode bacteriën of dode cellen en componenten of metabolisme voor het menselijk lichaam en andere organismen toxiciteit, sensibilisatie en andere biologische reacties, producttoxiciteit, sensibiliteit en andere biologische reacties, milieu, milieu Effecten.
Schone ruimte: een kamer (gebied) waar stofdeeltjes en microbiële besmetting in de omgeving moeten worden geregeld. De bouwstructuur, apparatuur en het gebruik ervan hebben de functie om de introductie, generatie en behoud van verontreinigende stoffen in het gebied te voorkomen.
Airlock: een geïsoleerde ruimte met twee of meer deuren tussen twee of meer kamers (zoals kamers met verschillende netheidsniveaus). Het doel van het opzetten van een luchtsluis is om de luchtstroom te regelen wanneer mensen of materialen binnenkomen en de luchtsluis verlaten. Airlocks zijn verdeeld in personeelsluchten en materiële luchtslakken.
De basiskenmerken van de schone kamer van biofarmaceuticals: stofdeeltjes en micro -organismen moeten de objecten zijn van omgevingscontrole. De netheid van de farmaceutische productieworkshop is verdeeld in vier niveaus: lokale klasse 100, klasse 1000, klasse 10000 en klasse 30000 onder de achtergrond van klasse 100 of klasse 10000.
De temperatuur van de schone kamer: zonder speciale vereisten, op 18 ~ 26 graden, en de relatieve vochtigheid wordt geregeld op 45%~ 65%. Vervuiling controle van biofarmaceutische schone workshops: broncontrole van vervuiling, diffusieprocescontrole en kruisbesmettingcontrole. De belangrijkste technologie van Clean Room Medicine is voornamelijk om stof en micro -organismen te regelen. Als verontreinigende stof zijn micro -organismen de topprioriteit van de milieucontrole van de schone kamer. De verontreinigende stoffen verzamelden zich in de apparatuur en pijpleidingen in het schone gebied van de farmaceutische fabriek, kunnen de medicijnen direct besmetten, maar heeft geen invloed op de netheidstest. Het netheidsniveau is niet geschikt voor het karakteriseren van de fysische, chemische, radioactieve en vitale eigenschappen van gesuspendeerde deeltjes. Niet bekend met het productieproces van geneesmiddelen, de oorzaken van vervuiling en de plaatsen waar verontreinigende stoffen zich ophopen, en de methoden en evaluatienormen voor het verwijderen van verontreinigende stoffen.
De volgende situaties zijn gebruikelijk in de GMP -technologie -transformatie van farmaceutische planten:
Vanwege het misverstand van subjectieve cognitie is de toepassing van schone technologie in het vervuilingscontroleproces ongunstig, en ten slotte hebben sommige farmaceutische planten veel geïnvesteerd in transformatie, maar de kwaliteit van geneesmiddelen is niet significant verbeterd.
Het ontwerp en de constructie van farmaceutische schone productie -fabrieken, de productie en installatie van apparatuur en faciliteiten in de fabrieken, de kwaliteit van ruwe en hulpmaterialen en verpakkingsmaterialen die bij de productie worden gebruikt, en de ongunstige implementatie van de controleprocedures voor schone mensen en schone faciliteiten zal de productkwaliteit beïnvloeden. De redenen die de productkwaliteit in de constructie beïnvloeden, zijn dat er problemen zijn in de procesbesturingsverbinding, en er zijn verborgen gevaren tijdens het installatie- en bouwproces, die als volgt zijn:
① De binnenwand van het luchtkanaal van het zuiverings airconditioningsysteem is niet schoon, de verbinding is niet strak en de luchtlekkage is te groot;
② De structuur van de kleurplaat van de kleur is niet strak, de afdichtingsmaatregelen tussen de schone kamer en de technische mezzanine (plafond) zijn onjuist en de gesloten deur is niet luchtdicht;
③ De decoratieve profielen en procespijpleidingen vormen dode hoeken en stofophoping in de schone kamer;
④ Sommige locaties zijn niet gebouwd volgens de ontwerpvereisten en kunnen niet voldoen aan de relevante vereisten en voorschriften;
⑤ De kwaliteit van het gebruikte afdichtmiddel is niet aan de standaard, gemakkelijk af te vallen en verslechteren;
⑥ De rendement en uitlaatkleurstalen plaatbanen zijn verbonden en stof komt het retourluchtkanaal uit de uitlaat binnen;
⑦ De binnenwandlas wordt niet gevormd bij het lassen van roestvrijstalen sanitaire leidingen zoals procesgezuiverd water en injectiewater;
⑧ De luchtkanaalcontroleklep werkt niet en de lucht terugstroom veroorzaakt vervuiling;
⑨ De installatiekwaliteit van het afvoersysteem is niet aan de standaard en het buisrek en de accessoires zijn gemakkelijk om stof te verzamelen;
⑩ De drukverschil van de schone kamer is ongekwalificeerd en voldoet niet aan de productieprocesvereisten.
Afdruk- en verpakkingsindustrie:
Met de ontwikkeling van de samenleving zijn de producten van de drukindustrie en de verpakkingsindustrie ook verbeterd. Grootschalige drukapparatuur is de cleanroom binnengekomen, die de kwaliteit van gedrukte producten aanzienlijk kan verbeteren en de gekwalificeerde producten aanzienlijk kan vergroten. Dit is ook de beste integratie van de zuiveringsindustrie en de drukindustrie. Afdrukken weerspiegelt voornamelijk de temperatuur en vochtigheid van het product in de omgeving van de coatingruimte, het aantal stofdeeltjes, en speelt direct een belangrijke rol in de productkwaliteit en gekwalificeerde snelheid. De verpakkingsindustrie wordt voornamelijk weerspiegeld in de temperatuur en vochtigheid van de ruimteomgeving, het aantal stofdeeltjes in de lucht en de kwaliteit van water in voedselverpakkingen en farmaceutische verpakkingen. Natuurlijk zijn de gestandaardiseerde operationele procedures van productiepersoneel ook erg belangrijk.
Stofvrij spuiten is een onafhankelijke workshop met gesloten productie die bestaat uit stalen sandwichpanelen, die de vervuiling van slechte luchtomgeving effectief naar producten kunnen filteren en stof in het spuitgebied en de productafdeling kunnen verminderen. De toepassing van stofvrije technologie verbetert verder de uiterlijkkwaliteit van producten, zoals tv/computer, mobiele telefoon shell, dvd/vcd, gameconsole, videorecorder, pda handheld computer, camera shell, audio, haardroger, md, make-up , speelgoed en andere werkstukken. Proces: Laadgebied → Handmatige stofverwijdering → Elektrostatische stofverwijdering → Handmatig/automatisch spuiten → Drooggebied → UV -verfverhardgebied → Koelgebied → Afdrukgebied van het scherm → Kwaliteitsinspectiegebied → Ontvangend gebied.
Om te bewijzen dat de stofvrije workshop van de voedselverpakking naar tevredenheid werkt, moet worden bewezen dat deze voldoet aan de vereisten van de volgende criteria:
① Het volume van de luchttoevoer van de stofvrije werkplaats voor voedselverpakkingen is voldoende om de binnenshuis gegenereerde vervuiling te verdunnen of te elimineren.
② De lucht in de stofvrije werkplaats van de voedselverpakking stroomt van het schone gebied naar het gebied met een slechte netheid, de stroom vervuilde lucht wordt geminimaliseerd en de luchtstroomrichting aan de deur en in het binnengebouw is correct.
③ De luchttoevoer van de stofvrije workshop voor voedselverpakkingen zal de binnenvervuiling niet significant verhogen.
④ De bewegingsstatus van de binnenlucht in de stofvrije werkplaats voor voedselverpakkingen kan ervoor zorgen dat er geen hoog-concentratie-verzamelgebied in de gesloten kamer is. Als de schone kamer voldoet aan de vereisten van de bovenstaande criteria, kan de deeltjesconcentratie of microbiële concentratie (indien nodig) worden gemeten om te bepalen dat deze voldoet aan de gespecificeerde Clean Room -normen.
Voedselverpakkingsindustrie:
1. Luchttoevoer en uitlaatvolume: als het een turbulente schone kamer is, moeten de luchttoevoer en uitlaatvolume worden gemeten. Als het een unidirectionele schone kamer is, moet de windsnelheid worden gemeten.
2. Luchtstroomregeling tussen zones: om te bewijzen dat de richting van de luchtstroom tussen zones correct is, dat wil zeggen dat het met een slechte netheid van het schone gebied naar het gebied stroomt, is het noodzakelijk om te testen:
① Het drukverschil tussen elke zone is correct;
② De richting van de luchtstroom bij de deur of openingen op de muur, vloer, enz. Is correct, dat wil zeggen, het stroomt van de schone ruimte naar het gebied met een slechte netheid.
3. Filterlekdetectie: het zeer efficiënte filter en het buitenste frame moeten worden geïnspecteerd om ervoor te zorgen dat gesuspendeerde verontreinigende stoffen niet doorgaan:
① beschadigd filter;
② De opening tussen het filter en het buitenste frame;
③ Andere delen van het filterapparaat en vallen de kamer binnen.
4. Lekdetectie van isolatie: deze test is om te bewijzen dat gesuspendeerde verontreinigende stoffen niet doordringen in de bouwmaterialen en de schone kamer binnendringen.
5. Binnen luchtstroomregeling: het type luchtstroomcontroletest hangt af van het luchtstroompatroon van de schone kamer - of deze nu turbulent of unidirectioneel is. Als de luchtstroom van de schone kamer turbulent is, moet worden geverifieerd dat er geen gebied is in de kamer waar de luchtstroom onvoldoende is. Als het een unidirectionele schone kamer is, moet worden geverifieerd dat de windsnelheid en windrichting van de hele kamer voldoen aan de ontwerpvereisten.
6. Suspende deeltjesconcentratie en microbiële concentratie: als de bovenstaande tests voldoen aan de vereisten, worden de deeltjesconcentratie en de microbiële concentratie (indien nodig) uiteindelijk gemeten om te controleren of ze voldoen aan de technische vereisten van het schone kamerontwerp.
7. Andere tests: Naast de bovengenoemde testen van de vervuilingscontrole, moeten soms een of meer van de volgende tests worden uitgevoerd: temperatuur; relatieve vochtigheid; binnenverwarming en koelcapaciteit; ruiswaarde; verlichting; trillingswaarde.
Farmaceutische verpakkingsindustrie:
1. Vereisten voor milieubeheersing:
① Bied het luchtzuiveringsniveau dat nodig is voor de productie. Het aantal luchtstofdeeltjes en levende micro -organismen in het zuiveringsproject van de verpakkingsworkshop moet regelmatig worden getest en opgenomen. Het statische drukverschil tussen verpakkingsworkshops van verschillende niveaus moet binnen de opgegeven waarde worden gehouden.
② De temperatuur en relatieve vochtigheid van het zuiveringsproject van de verpakkingsworkshop moeten consistent zijn met de vereisten van de productieproces.
③ Het productiegebied van penicillines, zeer allergene en anti-tumor medicijnen moeten worden uitgerust met een onafhankelijk airconditioningsysteem en het uitlaatgas moet worden gezuiverd.
④ Voor kamers die stof genereren, moeten effectieve stofafwijkingsapparaten worden geïnstalleerd om kruisbesmetting van stof te voorkomen.
⑤ Voor hulpproductiekamers zoals opslag, moeten de ventilatiefaciliteiten en temperatuur en vochtigheid consistent zijn met de vereisten van farmaceutische productie en verpakkingen.
2. Reinheid bestemmingsplannen en ventilatiefrequentie: de schone kamer moet strikt de luchtreinigheid regelen, evenals de parameters zoals omgevingstemperatuur, vochtigheid, vers luchtvolume en drukverschil.
① Het zuiveringsniveau en de ventilatiefrequentie van de farmaceutische productie- en verpakkingsworkshop De luchtreinigheid van het zuiveringsproject van de farmaceutische productie- en verpakkingsworkshop is verdeeld in vier niveaus: Klasse 100, klasse 10.000, klasse 100.000 en klasse 300.000. Om de ventilatiefrequentie van de schone kamer te bepalen, is het noodzakelijk om het luchtvolume van elk item te vergelijken en de maximale waarde te nemen. In de praktijk is de ventilatiefrequentie van de klasse 100 300-400 keer/u, Klasse 10.000 is 25-35 keer/u en de klasse 100.000 is 15-20 keer/u.
② Reinheid bestemmingsplannen van het cleanroom -project van de farmaceutische verpakkingsworkshop. De specifieke bestemmingsplannen van de netheid van de farmaceutische productie- en verpakkingsomgeving is gebaseerd op de nationale standaardzuiveringsstandaard.
③ Bepaling van andere omgevingsparameters van het Cleanroom -project van de verpakkingsworkshop.
④ Temperatuur en vochtigheid van het cleanroom -project van de verpakkingsworkshop. De temperatuur en relatieve vochtigheid van de schone kamer moeten voldoen aan het farmaceutische productieproces. Temperatuur: 20 ~ 23 ℃ (zomer) voor klasse 100 en klasse 10.000 netheid, 24 ~ 26 ℃ voor klasse 100.000 en klasse 300.000 netheid, 26 ~ 27 ℃ voor algemene gebieden. Klasse 100 en 10.000 netheid zijn steriele kamers. Relatieve vochtigheid: 45-50% (zomer) voor hygroscopische geneesmiddelen, 50% ~ 55% voor vaste preparaten zoals tabletten, 55% ~ 65% voor waterinjecties en orale vloeistoffen.
⑤ Clean kamerdruk om binnen de netheid binnen te behouden, positieve druk moet binnen worden gehandhaafd. Voor schone kamers die stof produceren, schadelijke stoffen en het produceren van penicilline-type sterk allergene geneesmiddelen, moet externe vervuiling worden voorkomen of moet relatieve negatieve druk worden gehandhaafd tussen gebieden. Statische druk van kamers met verschillende netheidsniveaus. De binnendruk moet positief worden gehouden, met een verschil van meer dan 5Pa uit de aangrenzende kamer, en het statische drukverschil tussen de schone kamer en de buitensfeer moet groter zijn dan 10 pa.
Voedselindustrie:
Voedsel is de eerste noodzaak van de mensen en ziekten komen uit de mond, dus de veiligheid en sanitaire voorzieningen van de voedingsindustrie spelen een belangrijke rol in ons dagelijks leven. De veiligheid en sanitaire voorzieningen van voedsel moeten voornamelijk worden gecontroleerd in drie aspecten: ten eerste de gestandaardiseerde werking van productiepersoneel; Ten tweede moet de bestrijding van externe milieuvervuiling (een relatief schone bedrijfsruimte worden vastgesteld. Ten derde moet de bron van inkoop vrij zijn van problematische productgrondstoffen.
Het gebied van de werkplaats voor voedselproductie is aangepast aan de productie, met een redelijke lay -out en soepele drainage; De workshopvloer is gebouwd met niet-slip, sterke, ondoordringbare en corrosiebestendige materialen, en is plat, vrij van waterophoping en schoon gehouden; De exit van de workshop en de drainage- en ventilatiegebieden die zijn verbonden met de buitenwereld zijn uitgerust met anti-rat-, anti-fly en anti-insect faciliteiten. De wanden, plafonds, deuren en ramen in de workshop moeten worden geconstrueerd met niet-toxische, lichtgekleurde, waterdichte, meedwedstieke, niet-schuur- en gemakkelijk te reinigen materialen. De hoeken van de muren, de gemalen hoeken en de bovenste hoeken moeten een boog hebben (de krommingstraal mag niet minder zijn dan 3 cm). De operatietabellen, transportbanden, transportvoertuigen en gereedschappen in de workshop moeten worden gemaakt van niet-giftige, corrosiebestendige, roestvrije, gemakkelijk te reinigen en desinfecteren en vaste materialen. Een voldoende aantal handwas-, desinfectie- en handdroogapparatuur of benodigdheden moet op geschikte locaties worden opgezet en de kranen moeten niet-manuele schakelaars zijn. Volgens de behoeften van productverwerking moeten er desinfectiefaciliteiten zijn voor schoenen, laarzen en wielen bij de ingang van de workshop. Er moet een kleedkamer zijn verbonden met de workshop. Volgens de behoeften van productverwerking moeten ook toiletten en doucheruimtes die op de workshop zijn verbonden, worden opgezet.
Opto -elektronica:
De cleanroom voor opto -elektronische producten is over het algemeen geschikt voor elektronische instrumenten, computers, halfgeleiderfabrieken, auto -industrie, ruimtevaartindustrie, fotolithografie, productie van microcomputers en andere industrieën. Naast luchtreiniging is het ook noodzakelijk om ervoor te zorgen dat aan de vereisten van statische elektriciteitsverwijdering wordt voldaan. Het volgende is een inleiding tot de stofvrije zuiveringsworkshop in de opto-elektronica-industrie, die de moderne LED-industrie als een voorbeeld neemt.
LED Cleanroom Workshop Project Installatie- en bouwcase-analyse: in dit ontwerp verwijst het naar de installatie van sommige zuiveringsvrije workshops voor terminalprocessen, en de zuivering van de zuivering is over het algemeen klasse 1.000, klasse 10.000 of klasse 100.000 cleanroom workshops. De installatie van cleanroomworkshops voor achtergrondverlichting is voornamelijk voor het stempelen van workshops, montage en andere cleanroomworkshops voor dergelijke producten, en de netheid ervan is over het algemeen klasse 10.000 of 100.000 cleanroom workshops. Binnenluchtparametervereisten voor LED Cleanroom Workshop Installatie:
1. Temperatuur- en vochtigheidseisen: de temperatuur is over het algemeen 24 ± 2 ℃ en de relatieve vochtigheid is 55 ± 5%.
2. Versluchtvolume: Aangezien er veel mensen in dit type schone stofvrije workshop zijn, moeten de volgende maximale waarden worden genomen volgens de volgende waarden: 10-30% van het totale luchttoevoervolume van de niet-unidirectionele cleanroom workshop; de hoeveelheid frisse lucht die nodig is om uitlaat binnenshuis te compenseren en de positieve drukwaarde binnen te behouden; Zorg ervoor dat het binnenste verse luchtvolume per persoon per uur ≥40 m3/u is.
3. Grote luchttoevoervolume. Om te voldoen aan de netheid en warmtebalans van warmte en vochtigheid in de cleanroom -workshop, is een groot volume van de luchttoevoer vereist. Voor een workshop van 300 vierkante meter met een plafondhoogte van 2,5 meter, als het een klasse 10.000 cleanroom workshop is, moet het luchttoevoervolume 300*2.5*30 = 22500m3/u zijn (de luchtveranderingsfrequentie is ≥25 keer/u ≥25 keer/u ); Als het een klasse 100.000 cleanroom workshop is, moet het volume van de luchttoevoer 300*2.5*20 = 15000m3/u zijn (de frequentie van de luchtverandering is ≥15 keer/u).
Medische en gezondheid:
Schone technologie wordt ook wel schone kamertechnologie genoemd. Naast het voldoen aan de conventionele vereisten van temperatuur en vochtigheid in kamers met airconditioning, worden verschillende engineering- en technische voorzieningen en strikt beheer gebruikt om het binnendeeltjesgehalte, de luchtstroom, de druk, enz. Binnen een bepaald bereik te regelen. Dit soort kamer wordt een schone kamer genoemd. Een schone kamer wordt gebouwd en gebruikt in een ziekenhuis. Met de ontwikkeling van medische en gezondheidszorg en hoge technologie wordt schone technologie breder gebruikt in medische omgevingen, en de technische vereisten voor zichzelf zijn ook hoger. Schone kamers die in de medische behandeling worden gebruikt, zijn voornamelijk verdeeld in drie categorieën: schone operatiekamers, schone verpleegkundige afdelingen en schone laboratoria.
Modulaire operatiekamer:
Modulaire operatiekamer neemt binnenmicro -organismen als het besturingsdoel, bedrijfsparameters en classificatie -indicatoren, en luchtreinigheid is een noodzakelijke garantieconditie. Modulaire operatiekamer kan worden onderverdeeld in de volgende niveaus volgens de mate van netheid:
1. Speciale modulaire operatiekamer: de netheid van de werkruimte is klasse 100 en de omgeving is klasse 1.000. Het is geschikt voor aseptische operaties zoals brandwonden, gewrichtsconversie, orgaantransplantatie, hersenchirurgie, oogheelkunde, plastische chirurgie en hartchirurgie.
2. Modulaire operatiekamer: de netheid van het operatiegebied is klasse 1000 en de omgeving is klasse 10.000. Het is geschikt voor aseptische operaties zoals thoracale chirurgie, plastische chirurgie, urologie, hepatobiliaire en pancreaschirurgie, orthopedische chirurgie en het ophalen van eieren.
3. Algemene modulaire operatiekamer: de netheid van de werkruimte is klasse 10.000 en de omgeving is klasse 100.000. Het is geschikt voor algemene chirurgie, dermatologie en buikchirurgie.
4. Quasi-Clean Modular Operation Room: De luchtreinigheid is klasse 100.000, geschikt voor verloskunde, anorectale chirurgie en andere operaties. Naast het netheidsniveau en de bacteriële concentratie van de schone operatiekamer, moeten de relevante technische parameters ook voldoen aan relevante voorschriften. Zie de belangrijkste tabel Technische parameters met kamers op alle niveaus in de schone operationele afdeling. De vliegtuigindeling van de modulaire operatiekamer moet worden verdeeld in twee delen: schoon gebieds- en niet-spijkantgebied volgens de algemene vereisten. De operatiekamer en de functionele kamers die rechtstreeks de operatiekamer serveren, moeten zich in een schone ruimte bevinden. Wanneer mensen en objecten door verschillende netheidsgebieden in de modulaire operatiekamer gaan, moeten luchtslakken, buffer kamers of pass -box worden geïnstalleerd. De operatiekamer bevindt zich meestal in het kerngedeelte. Het interne vlak en kanaalvorm moet voldoen aan de principes van functionele stroming en een duidelijke scheiding van schoon en vuil.
Verschillende soorten schone verpleegafdelingen in het ziekenhuis:
Schone verpleegkundige afdelingen zijn onderverdeeld in isolatieafdelingen en intensive care -eenheden. Isolatieafdelingen zijn verdeeld in vier niveaus volgens het biologische risico: P1, P2, P3 en P4. P1 -afdelingen zijn in principe hetzelfde als gewone afdelingen, en er is geen speciaal verbod op buitenstaanders die binnenkomen en verlaten; P2 -afdelingen zijn strenger dan P1 -afdelingen, en buitenstaanders zijn in het algemeen verboden om binnen te gaan en te verlaten; P3 -afdelingen worden van buiten naar buiten geïsoleerd door zware deuren of bufferkamers, en de interne druk van de kamer is negatief; P4 -afdelingen worden van de buitenkant gescheiden door isolatiegebieden en de negatieve druk binnenshuis is constant bij 30Pa. Medisch personeel draagt beschermende kleding om infectie te voorkomen. Intensive care-eenheden zijn onder meer ICU (intensive care-eenheid), CCU (cardiovasculaire patiëntenzorgeenheid), NICU (voortijdige kinderopvang), leukemie-kamer, enz. De kamertemperatuur van de leukemieruimte is 242, de windsnelheid is 0,15-0,3/ M/s, de relatieve vochtigheid is minder dan 60%, en de netheid is klasse 100. Tegelijkertijd moet de schoonste lucht die wordt geleverd eerst het hoofd van de patiënt bereiken, zodat de mond En het ademhalingsgebied van de neus ligt aan de luchttoevoer en de horizontale stroom is beter. De bacteriële concentratiemeting in de brandwijk toont aan dat het gebruik van verticale laminaire stroming duidelijke voordelen heeft ten opzichte van open behandeling, met een laminaire injectiesnelheid van 0,2 m/s, een temperatuur van 28-34 en een netheidsniveau van klasse 1000. Ademhalings- Orgel afdelingen zijn zeldzaam in China. Dit type afdeling heeft strikte vereisten voor binnentemperatuur en vochtigheid. De temperatuur wordt geregeld op 23-30 ℃, de relatieve vochtigheid is 40-60%en elke wijk kan worden aangepast volgens de eigen behoeften van de patiënt. Het netheidsniveau wordt gecontroleerd tussen klasse 10 en klasse 10000 en de ruis is minder dan 45 dB (a). Personeel dat de afdeling binnenkomt, moet persoonlijke zuivering ondergaan, zoals het veranderen van kleding en douchen, en de afdeling moet positieve druk behouden.
Laboratorium:
Laboratoria zijn verdeeld in gewone laboratoria en bioveiligheidslaboratoria. De experimenten uitgevoerd in gewone schone laboratoria zijn niet besmettelijk, maar de omgeving is vereist om geen nadelige effecten te hebben op het experiment zelf. Daarom zijn er geen beschermende faciliteiten in het laboratorium en moet de netheid voldoen aan de experimentele vereisten.
Een bioveiligheid laboratorium is een biologisch experiment met primaire beschermingsfaciliteiten die secundaire bescherming kunnen bereiken. Alle wetenschappelijke experimenten op het gebied van microbiologie, biomedicine, functionele experimenten en genrecombinatie vereisen bioveiligheidslaboratoria. De kern van bioveiligheidslaboratoria is veiligheid, die zijn verdeeld in vier niveaus: P1, P2, P3 en P4 volgens de mate van biologisch gevaar.
P1 -laboratoria zijn geschikt voor zeer bekende ziekteverwekkers, die niet vaak ziekten veroorzaken bij gezonde volwassenen en weinig gevaar vormen voor experimenteel personeel en het milieu. De deur moet tijdens het experiment worden gesloten en de operatie moet worden uitgevoerd volgens gewone microbiologische experimenten; P2 -laboratoria zijn geschikt voor ziekteverwekkers die matig potentieel gevaarlijk zijn voor mensen en het milieu. De toegang tot het experimentele gebied is beperkt. Experimenten die aerosolen kunnen veroorzaken, moeten worden uitgevoerd in kasten van klasse II en moeten autoclaven beschikbaar zijn; P3 -laboratoria worden gebruikt in klinische, diagnostische, onderwijs- of productiefaciliteiten. Werk gerelateerd aan endogene en exogene ziekteverwekkers wordt op dit niveau uitgevoerd. Blootstelling en inademing van de ziekteverwekkers zal ernstige en potentieel dodelijke ziekten veroorzaken. Het laboratorium is uitgerust met dubbele deuren of luchtslossen en een extern geïsoleerd experimenteel gebied. Niet-personeelsleden zijn verboden om binnen te komen. Het laboratorium is volledig negatief onder druk. Klasse II bioveiligheid kasten worden gebruikt voor experimenten. HEPA -filters worden gebruikt om binnenlucht te filteren en buitenshuis uit te putten. P4 -laboratoria hebben strengere vereisten dan P3 -laboratoria. Sommige gevaarlijke exogene ziekteverwekkers hebben een hoog individueel risico op laboratoriuminfectie en levensbedreigende ziekten veroorzaakt door aerosoloverdracht. Relevant werk moet worden uitgevoerd in P4 -laboratoria. De structuur van een onafhankelijk isolatiegebied in een gebouw en een externe verdeling wordt aangenomen. Negatieve druk wordt binnenshuis gehouden. Klasse III bioveiligheid kasten worden gebruikt voor experimenten. Airpartitie -apparaten en doucheruimtes zijn opgezet. Operators moeten beschermende kleding dragen. Niet-personeelsleden zijn verboden om binnen te komen. De kern van het ontwerp van bioveiligheidslaboratoria is dynamisch isolatie en uitlaatmaatregelen zijn de focus. Desinfectie ter plaatse wordt benadrukt en er wordt aandacht besteed aan de scheiding van schoon en vuil water om per ongeluk verspreiding te voorkomen. Matige netheid is vereist.
Posttijd: JUL-26-2024