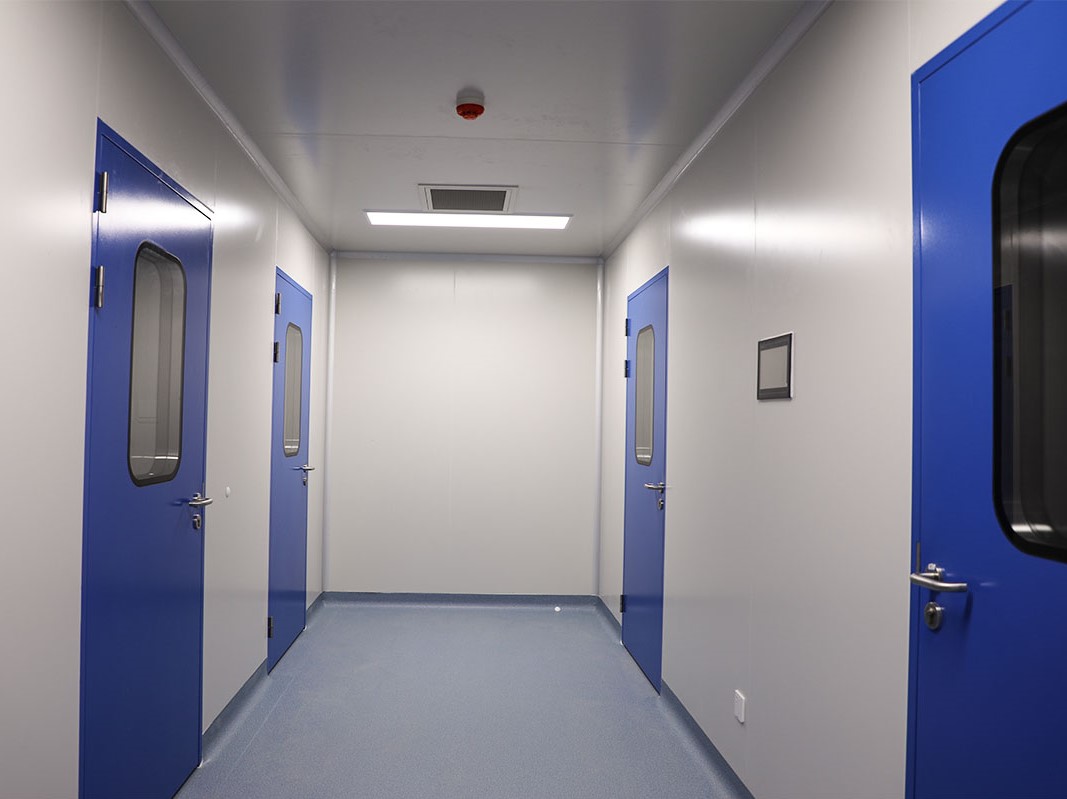
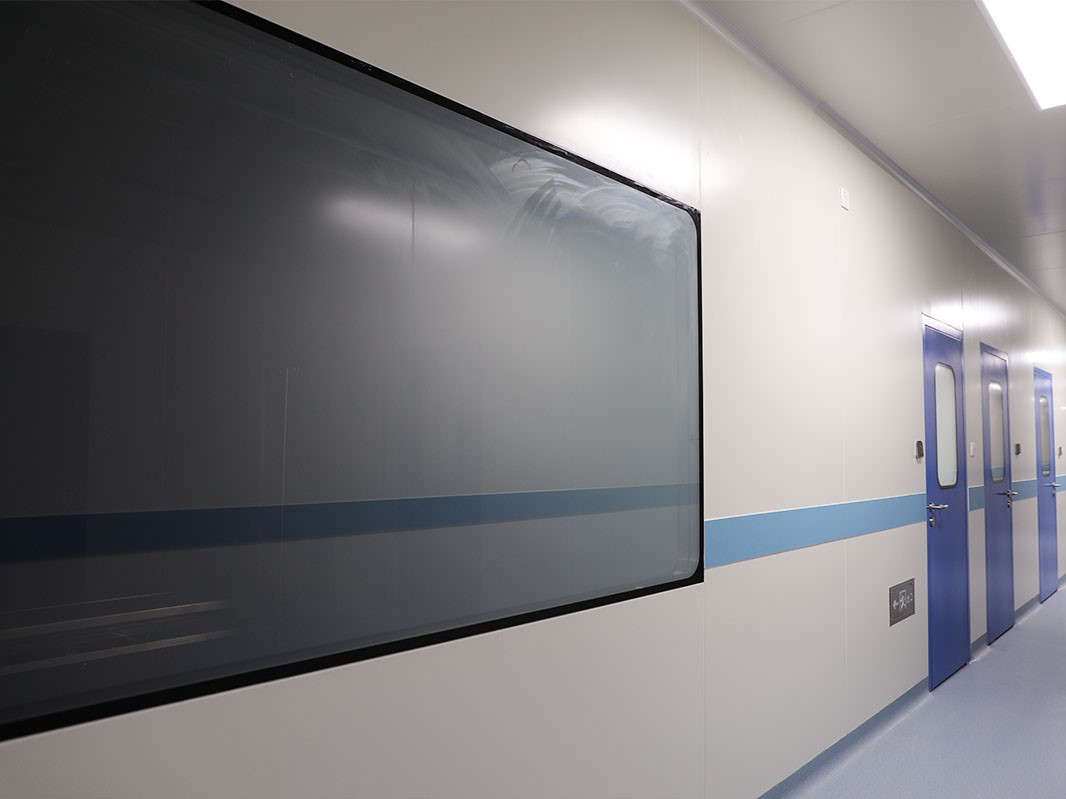
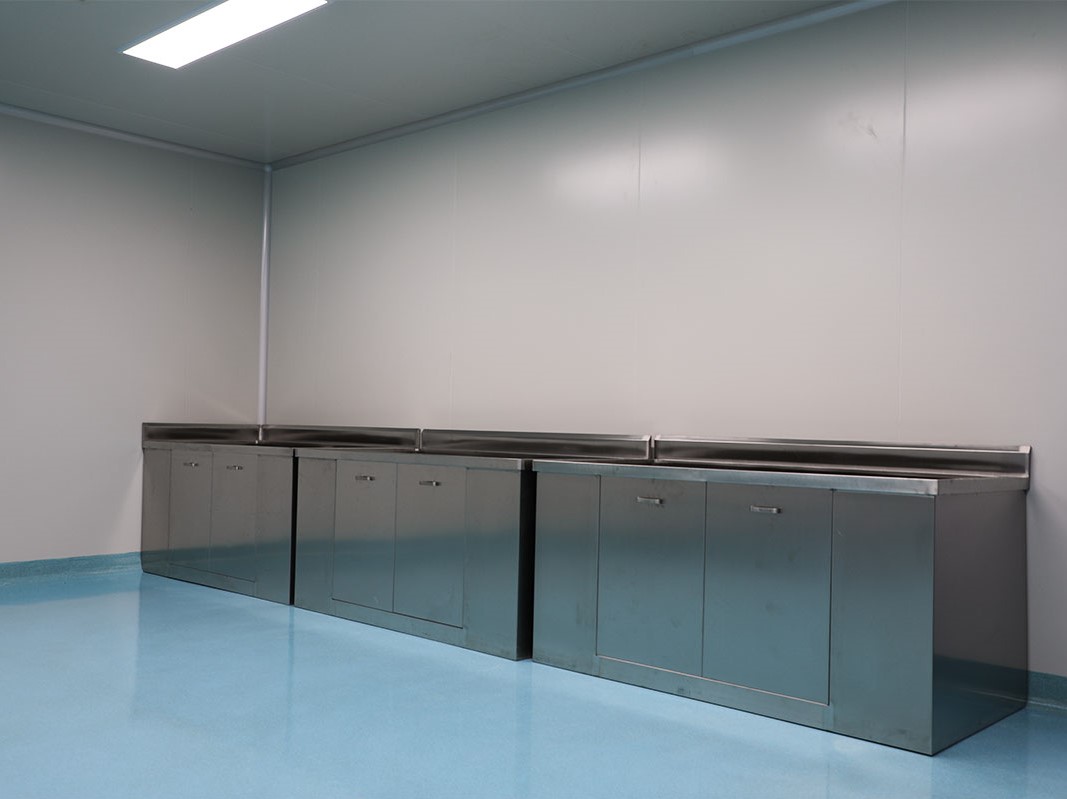
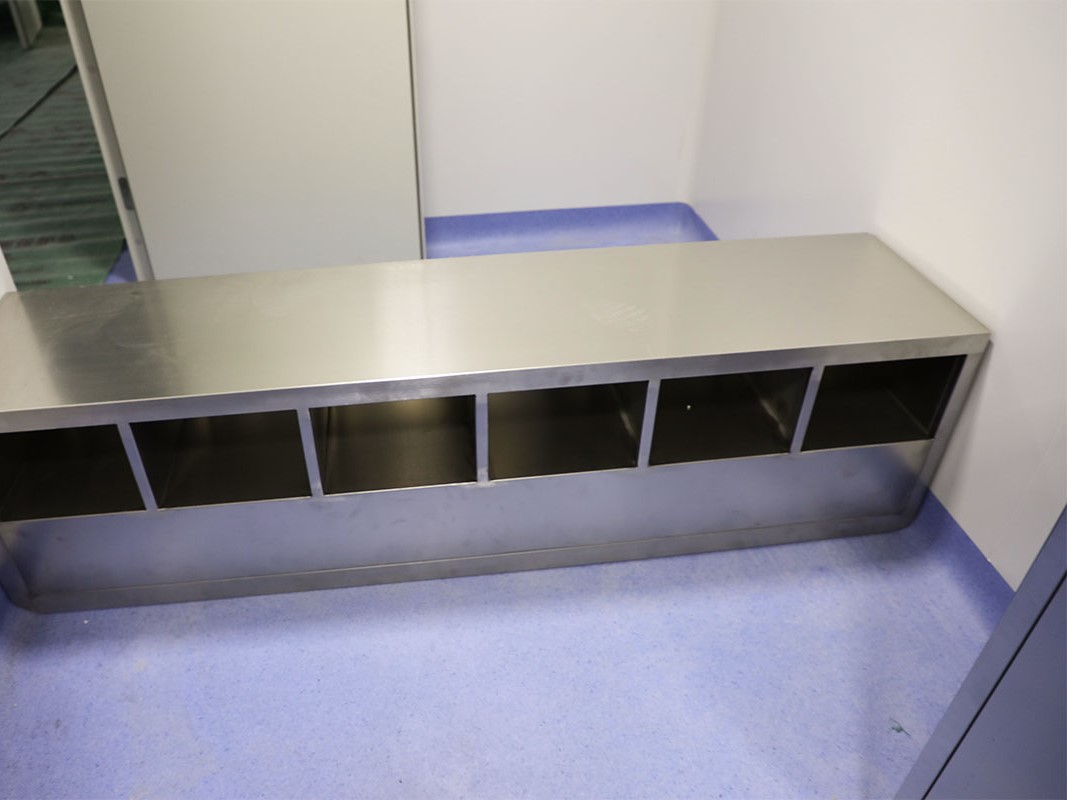
Sinds de afkondiging in 1992 is de "Good Manufacturing Practice for Drugs" (GMP) in de Chinese farmaceutische industrie geleidelijk erkend, geaccepteerd en geïmplementeerd door farmaceutische productie -ondernemingen. GMP is een nationaal verplicht beleid voor ondernemingen en ondernemingen die niet voldoen aan de vereisten binnen de gespecificeerde tijdslimiet zullen de productie stoppen.
De kerninhoud van GMP -certificering is de kwaliteitsmanagementcontrole van de productie van geneesmiddelen. De inhoud ervan kan worden samengevat in twee delen: softwarebeheer en hardwarefaciliteiten. Het Clean Room -gebouw is een van de belangrijkste investeringscomponenten in hardwarefaciliteiten. Na de voltooiing van het schone kamergebouw, of het nu de ontwerpdoelstellingen kan bereiken en aan de GMP -vereisten kan voldoen, moet uiteindelijk worden bevestigd door testen.
Tijdens de inspectie van een schone kamer faalden sommigen van hen de inspectie van de netheid, sommigen waren lokaal voor de fabriek, en sommige waren het hele project. Als de inspectie niet gekwalificeerd is, hoewel beide partijen de vereisten hebben bereikt door middel van rectificatie, foutopsporing, reiniging, enz., Verspilt het vaak veel mankracht en materiële middelen, vertraagt de bouwperiode en vertraagt het proces van GMP -certificering. Sommige redenen en defecten kunnen worden vermeden voordat ze worden getest. In ons werkelijke werk hebben we geconstateerd dat de belangrijkste redenen en verbeteringsmaatregelen voor ongekwalificeerde netheid en GMP -falen zijn onder meer:
1. Onredelijk engineeringontwerp
Dit fenomeen is relatief zeldzaam, voornamelijk bij de constructie van kleine schone kamers met lage reinheidseisen. De concurrentie in Clean Room Engineering is nu relatief hevig en sommige bouweenheden hebben lagere offertes in hun biedingen verstrekt om het project te verkrijgen. In de latere fase van de constructie werden sommige eenheden gebruikt om hoeken te snijden en lagere stroom airconditioning en ventilatiecompressoreenheden te gebruiken vanwege hun gebrek aan kennis, wat resulteerde in niet -overeenkomende voedingskracht en een schone oppervlakte, wat resulteerde in ongekwalificeerde netheid. Een andere reden is dat de gebruiker na het begin van het ontwerp en de bouw van nieuwe vereisten en schoon gebied heeft toegevoegd, waardoor het oorspronkelijke ontwerp ook niet in staat is om aan de vereisten te voldoen. Dit aangeboren defect is moeilijk te verbeteren en moet worden vermeden tijdens de technische ontwerpfase.
2.. Vervanging van hoogwaardige producten door low-end producten
Bij de toepassing van HEPA-filters in schone kamers bepaalt het land dat voor luchtzuiveringsbehandeling met een netheidsniveau van 100000 of hoger, drie niveaus filtratie van primaire, medium en HEPA-filters moet worden gebruikt. Tijdens het validatieproces werd vastgesteld dat een groot schone kamerproject een Sub HEPA -luchtfilter gebruikte om het HEPA -luchtfilter te vervangen op een netheidsniveau van 10000, wat resulteerde in ongekwalificeerde netheid. Ten slotte werd het zeer efficiënte filter vervangen om te voldoen aan de vereisten van GMP-certificering.
3. Slechte afdichting van het luchttoevoerschakel of filter
Dit fenomeen wordt veroorzaakt door ruwe constructie en tijdens acceptatie kan het lijken dat een bepaalde kamer of een deel van hetzelfde systeem niet gekwalificeerd is. De verbeteringsmethode is om de lektestmethode voor het luchttoevoerkanaal te gebruiken en het filter gebruikt een deeltjesbalie om de dwarsdoorsnede, afdichtlijm en installatiekader van het filter te scannen, de lekkage te identificeren en zorgvuldig af te dichten.
4. Slecht ontwerp en inbedrijfstelling van terugkeerluchtkanalen of luchtopeningen
In termen van ontwerpredenen, soms vanwege ruimtebeperkingen, is het gebruik van "Top Supply Side Return" of onvoldoende aantal terugkeerluchtopeningen niet haalbaar. Na het elimineren van ontwerpredenen is het foutopsporing van retourluchtopeningen ook een belangrijke bouwverbinding. Als het debuggen niet goed is, is de weerstand van de terugbladen voor de retourlucht te hoog en is het retourluchtvolume minder dan het luchtvolume van de voedingslucht, het zal ook ongekwalificeerde netheid veroorzaken. Bovendien beïnvloedt de hoogte van de retourluchtuitlaat uit de grond tijdens de bouw ook de netheid.
5. Onvoldoende zelfzuiveringstijd voor het Clean Room System tijdens het testen
Volgens de nationale norm moet de testinspanning 30 minuten worden gestart nadat het zuiverings airconditioningsysteem normaal werkt. Als de looptijd te kort is, kan dit ook ongekwalificeerde netheid veroorzaken. In dit geval is het voldoende om de bedrijfstijd van het airconditioning -zuiveringssysteem op de juiste manier te verlengen.
6. Het zuiverings airconditioningsysteem is niet grondig gereinigd
Tijdens het bouwproces wordt het gehele zuiverings airconditioningsysteem, met name de leverings- en retourluchtkanalen, niet in één keer voltooid en kan bouwpersoneel en de bouwomgeving vervuiling veroorzaken voor de ventilatiekanalen en filters. Als het niet grondig wordt gereinigd, heeft dit rechtstreeks invloed op de testresultaten. De verbeteringsmaatregel is schoon te maken tijdens het bouwen, en nadat het vorige deel van de pijpleidinginstallatie grondig is gereinigd, kan plastic film worden gebruikt om het te verzegelen om vervuiling veroorzaakt door omgevingsfactoren te voorkomen.
7. Schone werkplaats niet grondig schoongemaakt
Ongetwijfeld moet een schone workshop grondig worden gereinigd voordat het testen kan doorgaan. Vereist dat het laatste veegpersoneel schone werkkleding draagt voor het reinigen om verontreiniging te elimineren veroorzaakt door het menselijke lichaam van het reinigingspersoneel. Reinigingsmiddelen kunnen kraanwater, zuiver water, organische oplosmiddelen, neutrale wasmiddelen, enz. Zijn voor mensen met antistatische vereisten, vegen grondig met een doek gedompeld in antistatische vloeistof.
Posttijd: JUL-26-2023